High Hydrostatic pressure
The high pressure equipment we set up in our laboratory allows us to explore a wide working field that, until now, was restricted to a few groups, given the scarce availability of the heavy instrumentation which was, traditionally, associated with the use of high pressure (belt-type or multi-anvil type presses, with working pressures of 4-10 GPa).
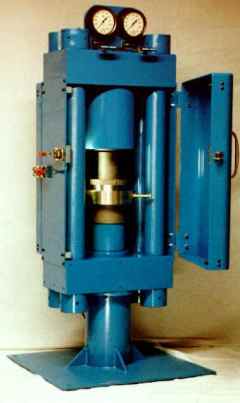
Our piston-cylinder hydrostatic press, from Rockland Research inc., allows us to work in a pressure range up to 3.5 GPa. Its utilization is relatively simple and allows us to set up an experiment within 1-2 hours.
Besides, the low cost per experiment (typically ~60 €) is about five times lower than the corresponding to multi-anvil of belt-types, which enables a much more systematic exploration of the pressure/composition space, very useful in the process of research of new crystallographic phases.
The samples are contained in gold or platinum capsules, made in our laboratory from 0.15 mm sheets of these metals. We have optimized and improved the experimental system proposed by the Rockland Company, in order to increase up to a maximum the available sample volumes. At present, we work with volumes of, typically, 0.15 cm3 (working at 2 GPa), or 0.08 cm3 (working at 3.5 GPa).
After reaching the working pressure in cold, the reactants are heated, under pressure, during periods in general no longer than 2 hours. Finally, the high pressure phases are quenched by cooling abruptly the sample before releasing pressure. In this way, we can perform a systematic analysis of the present oxides in the available range of pressure and temperature, in order to elaborate a (P,T) phase diagram of the system under study. The nature and purity of the products will be determined by X-ray diffraction.
We usually carry out two distinct types of reactions under hydrostatic pressure: i) those proceeding in the presence of high oxygen pressure, which is achieved by mixing the reactants with KClO4 (30-40% in weight), that generates O2 in-situ within the gold capsule (probably atomic oxygen, very reactive) and ii) those reactions which do not require the presence of an oxidizing agent, in such a way that the hydrostatic pressure simply avoids the decomposition of the reactants or the formed oxides.
In the conditions of i) we prepare the RNiO3 perovskites with a higher degree of distortion (R= Y, Ho…Lu), as well the Mn oxides of the system CaCu3Mn4O12 and some of its derivatives. In the conditions of ii) the perovskites containing p elements in reduced oxidation states (Sn2+, Bi3+, Se4+…) are prepared from the simple oxides with the adequate oxygen contents, in such a way that any unwanted oxidation-reduction processes are prevented.
High oxygen pressure (up to 30 MPa at 900ºC)
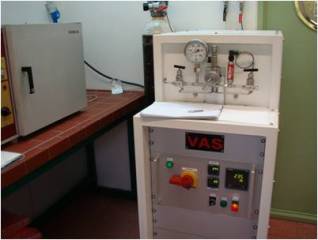
There are two oxygen-pressure furnaces in our Laboratory; one of Morris Research inc. (20 MPa= 200 bar) and the second from VAS (30 MPa O2). The high-oxygen pressure furnaces are adequate to stabilize some of the members of the nickel perovskites, RNiO3, and some of their derivatives (e.g. RNi1-xMnxO3) in particular for the large-to-medium sized rare earths.
For a correct oxygenation it is essential to start from finely divided precursor powders, generally obtained by citrate techniques. The previously obtained precursors, decomposed in air at moderate temperatures, are introduced in the high O2 pressure reactor within gold sample holders. A programmed slow cooling improves the oxygenation of the materials.